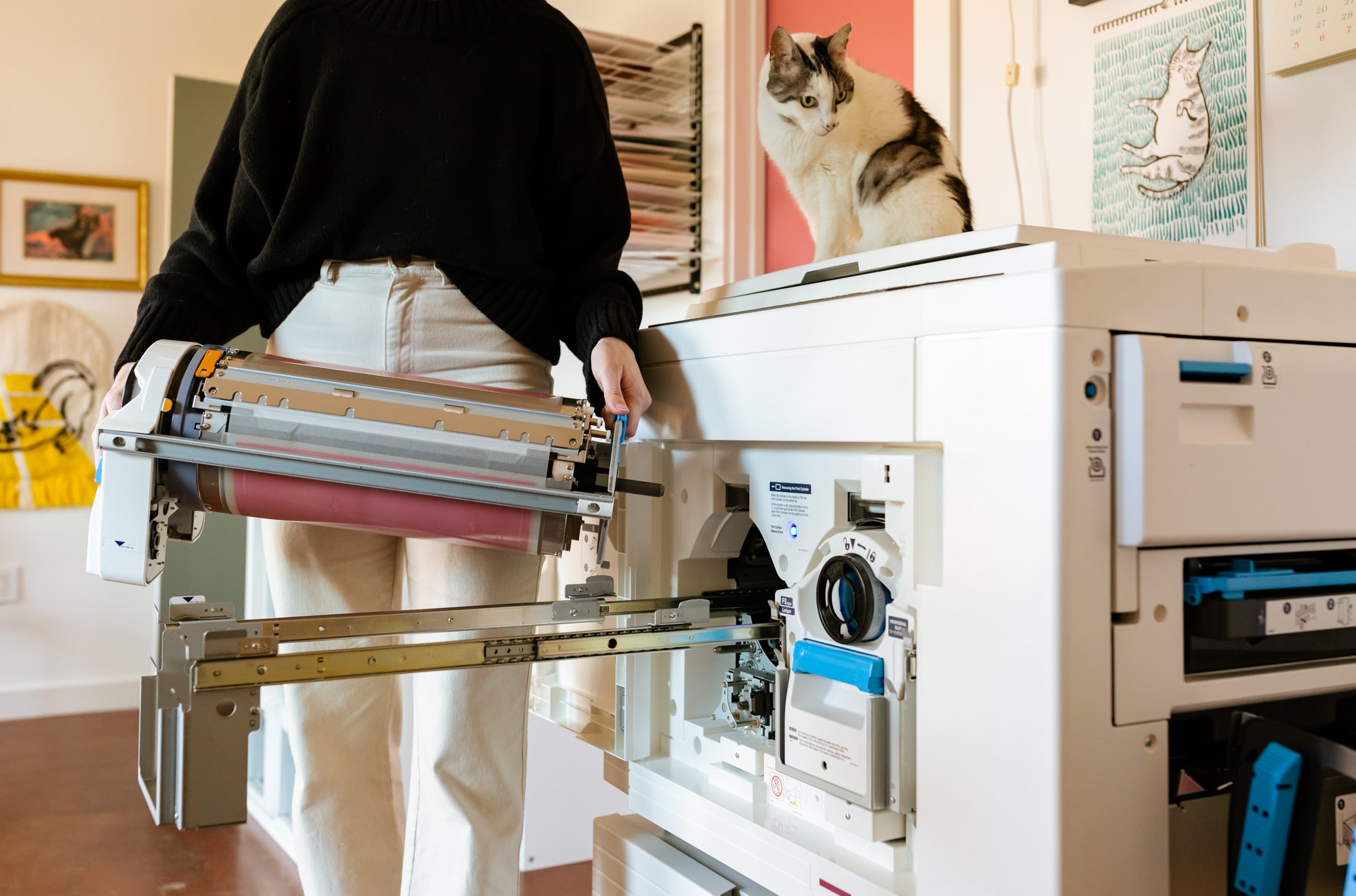
What is risograph printing?
Risograph printing is sometimes called "digital screen printing" and works based on the same stencil concept as traditional screen printing.
Although it may look like a photocopier from the outside, a risograph machine does not require heat or toner, instead using rice paper stencils and soy-based inks to create its unmistakable grainy, slightly misregistered prints on smooth, uncoated papers.
Risograph machines were invented in the 80's as a cost-effective, high volume printing solution for places like offices, schools, and churches.
More recently, artists and designers have adopted risograph printing for the charming analog feel of the prints. Each color ink requires its own dedicated ink drum, which means every risograph studio will have its own curated palette of inks to print with.
BPC prints on a two-drum model machine, meaning that for every two additional colors in the print, the paper had to pass through the machine another time.
It's nearly impossible to perfectly register each ink layer because of slight shifting throughout the printing process, but the imperfections between prints becomes what makes them unique. Risograph printing has an inimitable vibrancy and immediacy that can't be captured by traditional, four-color commercial printing processes.